U series
U5 / U8
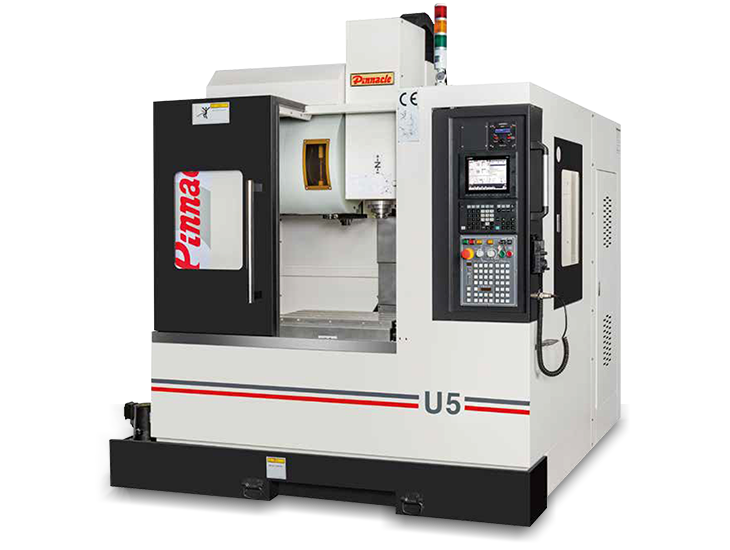
Ultrasonic spindle serie
Highly rigid structural design, equipped with ultrasonic spindle, creates perfect fast cutting quality.
- Excellent for machining brittle, extra hard, and tough materials
- Applicable for precision machining of conductive metallic materials and non-conductive, non-metallic brittle materials, such as glass, ceramics, semiconductors, etc
- Upgrade defect-free rate and throughput
- Improve machining surface finish and reduce need for polishing process
- Help to reduce cutting stress while extending tool service life
- Rigid, Stable, Accurate
- Specifications
- Accessories
- Application
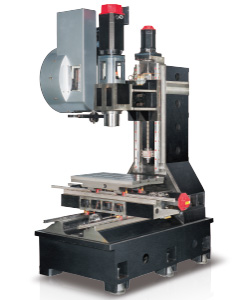
U5 / U8
HIGHLY RIGID STRUCTURE
EQUIPPED WITH AN ULTRASONIC SPINALE TO
CREATE PERFECT QUALITY IN HIGH SPEED MACHIRLIJNG.
- All structural parts are manufactured from high quality Meehanite cast iron (FC30) and hardened to a hardness over HB 190, then tempered to relieve internal stress
- Three axes are fitted with high precision P class linear ways with oversized blocks
- Width of linear way: 30mm
- Back mount chip exhaust system for saving space
- Class C3 high precision ballscrews on three axes
- Ballscrew diameter: 32mm
- Powerful high performance AC servomotor drive enable 36 m/min of rapid traverse rate. Smooth movement combined with powerful drive to assure fine finishes on machined surfaces
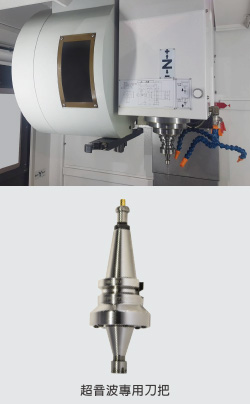
ULTRASONIC MACHINES EQUIPPED WITH ADVANCED ULTRASONIC SPINDLES ARE THE BEST CHOICE FOR PROCESSING HARD AND BRITTLE MATERIALS AND DIFFICULT-TO-CUT MATERIALS.
- Non-contact electricity transfer. electric energy transfer efficiency can reach 93%
- 24,000 RPM high speed spindle
- Outstanding spindle rigidity
- Providing total solutions in ultrasonic machining
- Dynamic balance grade: G0.4
- With the use of amplitude measuring device (optional), controller and driver execute tool amplitude feedback system, thus acheving automated machining
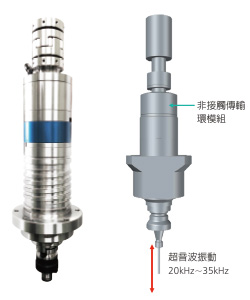
ULTRASONIC SPINDLE MODULE
HIGH FREQUENCY VIBRATION, HIGH PRECISION.
OUTSTANDING FEATURES:
- Non-contact (wireless) electricity transfer. High efficiency electric energy transfer
- Range of axial too丨vibration frequency: 20-35 KHz
- Range of amplitude: 1-14 µm (automatic frequency sweep)
- Tool accuracy can reach to within 5 µm
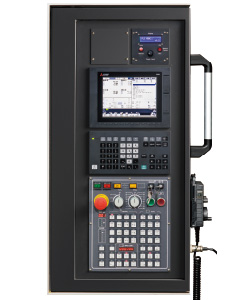
USER-FRIENDLY HUMAN-MACHINE INTERFACE
- Mitsubishi CNC M80 controller
- 1 0.4" color LCD
- High speed program server and Ethernet
- 10 nanometer interpolation control
- All servo/ spindle drivers employ optical fiber communication
- The resolution of servo detector can be upgraded by four times
- High quality operation keyboard
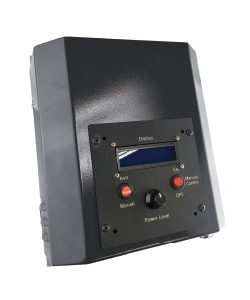
ULTRASONIC DRIVER
- Max. Power: 60W
- Range of frequency sweep: 20 KHz-35 KHz
- 35 KHz-42 KHz
- Max. input voltage: 220 VAC/24 VDC
- Max. output voltage: 200 VAC
- Amplitude control range: 30-1 00%
- Protection: Over-voltage and over-current protection
- POWER SWITCH
- Communicate with various brands of controller through 1/0 Vibration amplitude 1-14 µm
- Frequency: 20 KHz-35 KHz
- Automatic frequency sweeping, pairing, and tracing
MODEL | U5 | U8 |
---|---|---|
TABLE | ||
Table Size | 660 x 410 | 910 x 510 |
Travel Ranges (X/Y/Z mm) | 510 / 410 / 510 | 810 / 510 / 510 |
Max. Table Load (kgs) | 300 | 300 |
Spindle Nose to Table Surfac (mm) | 150~660 | 150~660 |
T Slot Size | 14 x 125 x 3 | 14 x 125 x 4 |
SPINDLE | ||
Tool Shank & Pull Stud | BT30 | BT30 |
Spindle Inner Diameter (mm) | Direct drive = Ø45 | Direct drive = Ø45 |
Spindle center to Column (mm) | 462 | 562 |
Spindle Max Speed (rpm) Direct Drive | 24000 | 24000 |
Clamping Force (kgf)) | 250 | 250 |
Spindle Power (con/30min kW) | 3.7 / 5.5 | 3.7 / 5.5 |
AXIS SERVO MOTOR | ||
Rapid Feed Rate (X/Y/Z m/min) | 48 | 48 |
Cutting Speed (X/Y/Z/ mm/min) | 20000 | 20000 |
X/Y/Z Axes Power (kW) | 1.5 / 1.5 / 2.0 | 1.5 / 1.5 / 2.0 |
X/Y/Z Axes Torque (Nm) | 4.8 / 4.8 / 6.4 | 4.8 / 4.8 / 6.4 |
AUTO TOOL CHANGER | ||
Cam Type | ARM | ARM |
Tool Selection (Bi-Direction) | RANDOM | RANDOM |
Tool Storage Capacity (PCs) | 20 | 20 |
Max. Tool Diameter (mm) | Ø 75 | Ø 75 |
Max. Tool Length (mm) | 150 | 150 |
Max. Tool Weight (kgs) | 4 | 4 |
MISCELLANEOUS | ||
Air Requirement (Kg/cm2) | 6 | 6 |
Voltage (v) | 220 | 220 |
Power Requirement (KVA) | 15 | 15 |
Coolant Tank Capacity (L) | 150 | 150 |
Machine Weight (kgs) | 3400 | 3600 |
Machine Height (mm) | 2815 | 2815 |
Floor Space (L x W mm) | 1700 x 2250 | 2200 x 2380 |
All Specifications And Designs Are Subject To Change Without Notice.
Ultrasonic Machining Applications
- Ultrasonic machining is suitable for various materials, including hard, brittle, and hard-to-cut materials, conductive and non-conductive materials
- For example: Glass, ceramic, (aluminum oxide, silicon nitride) quartz, silicon, graphite, jewel, hard alloy, stain丨ess steel, silicon carbide and carbon fiber board, etc
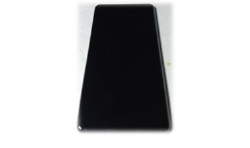
Zirconia Machining
Mohs' hardness 8.5
- Takes 38 min 12 sec to process a raw
block (132.5g) to a finished goods (44g) - Removal rate : 2.329g/min (Total:88.Sg)
- Ra: 0.087 um / Rz: 0.534um
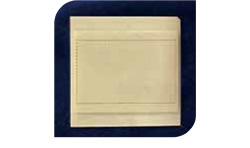
Aluminum Nitride Machining
Mohs' hardness 7
- Takes 2 min 2 sec to drill a 1 mm depth hole
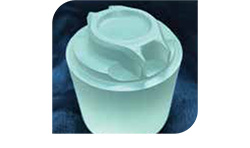
Jewel Machining
Mohs' hardness 9
- 98 min from raw blank to finishing goods.
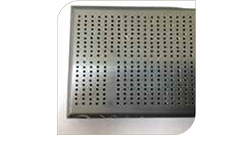
Monocrystalline Silicon Machining
Mohs' hardness 7
- Planar milling to 0.05 mm depth with 02, grain size 200 tool
- Milling square groove to 0.05 mm depth with 02, grain size 200 tool Drill a 00.45, 10mm depth, 1 min 15 sec
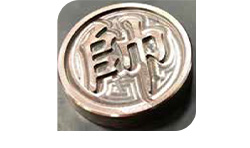
Tungsten Copper Composite Machining
Hardness 250 - 350
- From a blank to a circle, 11 min 4 sec
- lanar milling, 1 min 42 sec Takes 37 min 8 sec for帥
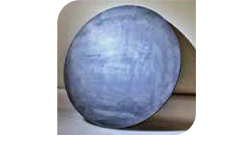
Silicon Carbide Machining
Mohs' hardness 9.5
- Drill a 042, 5.9 mm depth hole, 40 sec
APPLICABLE INDUSTRIES
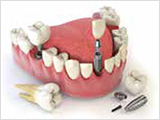
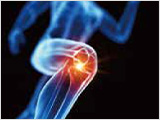
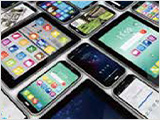
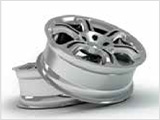
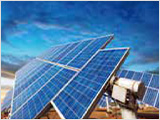
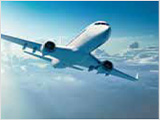