LV series
LV116/LV126
LV's Designed for Extra Value and Built for Optimum Performance
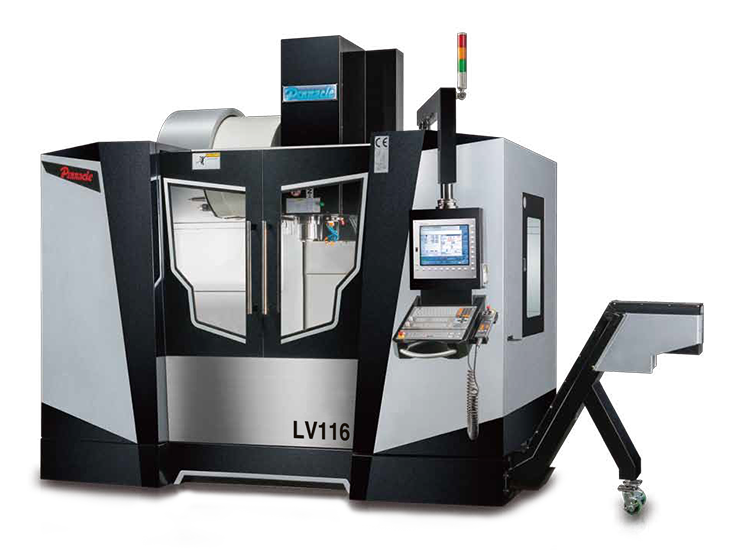
Linear Way Series
When jobs call for highly efficient machining and when outstanding accuracy is critical, a Pinnacle linear way series vertical machining center is the perfect solution. The three axes move on linear guideways that minimize friction while providing high accuracy of positioning and repeatability. This series are not only suitable for larg-range production line application. It is also ideal for smaller factories and machine shops. If you are serious about increasing machining productivity and profits, the Pinnacle linear way series LV can really help you.
Features
- 1140(1270) X 610 x 610 mm Travel
- Rapid Feedrate 30/30/24 m/min
- 15 HP Spindle Motor
- ISO40 (ISO50) Spindle Taper
- Spindle Speed 8,000 rpm, 10,000 rpm (option)
- Direct drive 12,000 rpm (option)
- X, Y & Z Axis Linear Way
- Features
- Specifications
- Accessories
- Quality Inspections
- Options
- Video
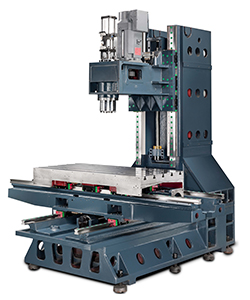
The Best Possible Structural Design
Rugged Construction Assures Optimum Rigidity and Stability.
The major structural parts are manufactured from high quality Meehanite cast iron (GB 300), tempered for stress relief with hardness over 190HB.
High precision and premium quality P class linear quidways way wide block and 35mm (LV85/LV105) and 45mm (LV116/LV126)width linear quideways on three axes.
Three axes equipped with class C3 precision and 36mm (LV85/LV105) and 40mm (LV116/LV126)diameter ball screws.
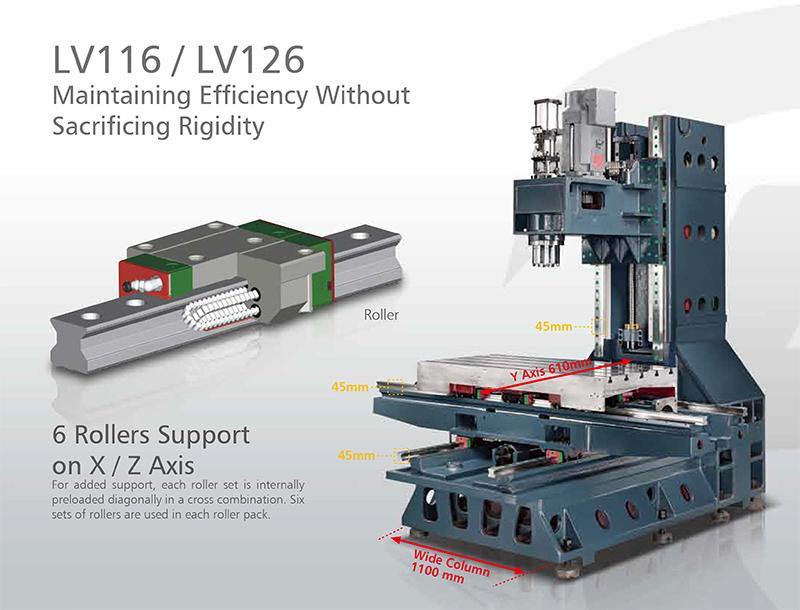
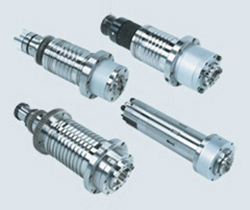
RIGID, PRECISION SPINDLE
ASSURES HIGH QUALITY MACHINING
- Supported by superior precision P4 class bearings, the spindle provides an extra wide range of machining capacity and high speed.
- Floating unclamping system assures tool unclamping force will not transmit to the spindle bearings. It provides stable tool clamping and unclamping with the spindle and extends the spindle bearings' life.
- The spindle is a cartridge-type.
- Choice of various spindle speeds - 8,000, 10,000 and 12,000 rpm.
- The circulating oil cooling system on the spindle head prevents thermal expansion and offers the best precision machining environment.
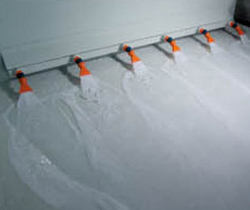
Chips Flushing Nozzles
Coolant flushing nozzles on rear inner wall of guard prevent jam of chips during operation.
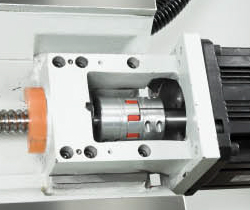
Couplings
Directly connected with ball screw and AC servo motors, the high precision flexible couplings offer the best rigidity and keeps the accuracy of axial linear assembly under high speed movement.
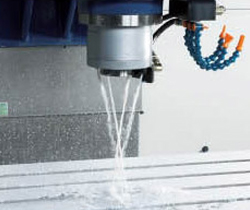
Coolants Jets Around Spindle
Improved cooling efficiency on workpiece.
Automatic Lubrication System
The Lubrication System automatically measures and accurately distributes the oil to the slide ways, ballscrews and bearings.
Control System
The centralized control panel employs a touch sensing screen for user-friendly operation. The humanized designed control panel has an elegant appearance. Various controllers can be chose - Mitsubishi, Heidenhain, Fanuc and Siemens.
Splash Guard
The full-enclosed splash guard meets environmental protection and CE requirements. It offers users a comfortable working environment.
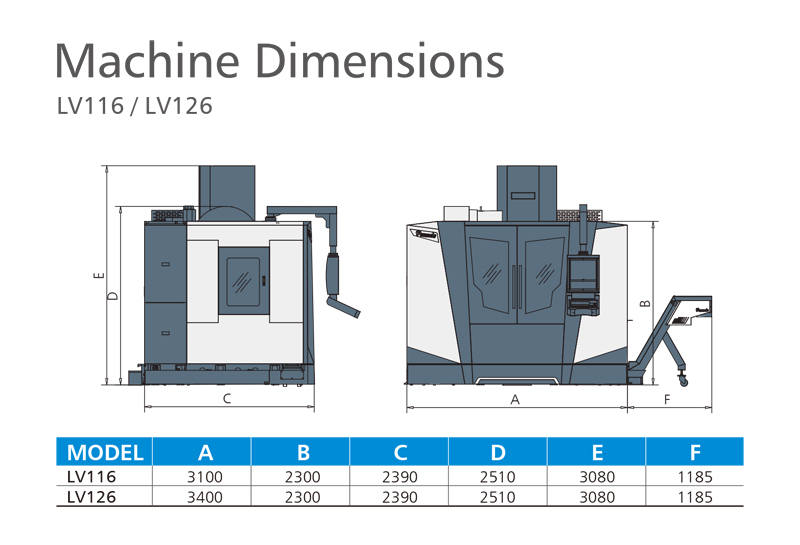
MODEL | LV116 | LV126 | ||
---|---|---|---|---|
TABLE | ||||
Table Size (mm) | 1300 x 610 | 1440 x 610 | ||
Travel Ranges (X x Y x Z mm) | 1140 x 610 x 610 | 1270 x 610 x 610 | ||
Max. Table Load (kgs) | 850 | 850 | ||
Spindle Nose to Table Surface (mm) | 120-730 | 120-730 | ||
T-slot (Width x Distance x Number mm) | 18 x 125 x 5 | 18 x 125 x 5 | ||
SPINDLE | ||||
Distance Between Column (mm) | BT-40 | BT-50 | ||
Spindle Inner Diameter (mm) | Ø70 | Ø80 | ||
Spindle Center to Column (mm) | 675 | 675 | ||
Spindle Speed (rpm) Belt | 60 ~ 8000(10000/12000) | 60 ~ 8000 | ||
Spindle Speed (rpm) Gear | L40~2000, H2001~8000 | L40~1500, H1501~6000 | ||
Spindle Speed (rpm) Direct-Drive | 10000 / 12000 / 15000 | 10000 | ||
Draw Bar Force (kgf) | 950 | 2000 | ||
Main Motor (con/30 min Kw) | 7.5 / 11 | 11 / 15 | ||
FEED RATE | ||||
Rapid Feed Rate (X/Y/Z m/min) | 30 / 30 / 24 | 30 / 30 / 24 | ||
Feed Rate (X/Y/Z/ mm/min) | 10000 | 10000 | ||
AXIS SERVOMOTOR | ||||
Mitsubishi X/Y/Z (Kw) | HF354 | HF354 | ||
Fanuc (Kw) | β22/3000is 3.0 (α12i/3000i 3.0) | |||
Siemens (Kw) | 1FK7 063 (2.9) | 1FK7 063 (2.9) | ||
Fagor (Kw) | FKM64.30A | FKM64.30A | ||
Heidenhain (Kw) | QSY155B (2.47) | QSY155B (2.47) | ||
AUTO TOOL CHANGER | ISO40 | ISO50 | ||
ATC Type | DISK | |||
Cam Type | DAUL ARM | |||
Tool Selection (Bi-direction) | RANDOM | |||
Tool Storage Capacity (PCs) | 24 | 24 | ||
Max. Tool Diameter (mm) | Ø90 | Ø105 | ||
Max. Tool Length (mm), Weight (kgs) | 250, 8 | 300, 15 | ||
MISCELLANEOUS | ||||
Air Requirement (Kg/cm2) | 6 | 6 | ||
Voltage | 220 | 220 | ||
Power Requirement (KVA) | 20 | 20 | ||
Coolant Tank Capacity (L) | 300 | 300 | ||
Machine Weight (Kgs) | 6500 | 6800 | ||
Machine Height (mm) | 2950 | 2950 | ||
Floor Space (L x W mm) | 3100 x 2230 | 3400 x 2230 | ||
Packing Size (L x W x H mm) | 3450 x 2300 x 2530 | 3450 x 2300 x 2530 |
All Specifications And Designs Are Subject To Change Without Notice.
Accessories
- Air blast through spindle
- Air blast for workpiece (nose)
- Coolant flushing system
- 3 axes telescopic covers
- Full splash guard
- Centralized automatic lubrication system
- Working lamp
- Operation status light
- Cooling system
- Air gun and water spray-gun
- MPG handwheel
- Heat exchanger
- RS-232 Interface
- Rigid tapping
- Spindle oil cooler
- Adjusting tools and box
- Leveling bolts and pads
- Operation and programming manual
Control System
- MITSUBISHI M80 / M830
- FANUC 0i-MF / 31i-MB
- HEIDENHAIN TNC620 / TNC640
- SIEMENS 828D / 840D
- FAGOR 8055i Plus / 8060FL / 8060
Quality Through Precision Inspections
Each Pinnacle machine is subject to dynamic and static accuracy tests.
Pinnacle machine accuracy meets VDI 3441, ISO 10791, JIS B6336 and ASMEB5 standards.
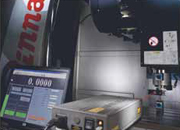
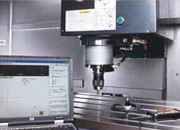
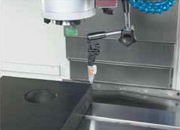

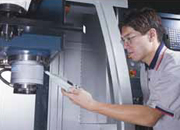
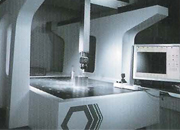
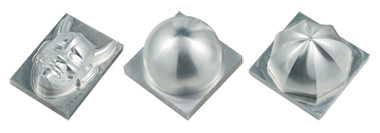